PLEASE!
Do not comment on this thread until I post after more testing this weekend. Thanks.
This should be titled:
“Having no welding experience, can you buy a flux core welder and, with a bit of practice, weld inner/outer sills to a decent standard.”
But that’s a bit long.
Matt Barnes is giving it a go in his progress thread. I can weld more than a bit, I’m not an expert, or Pro, and I’ve been offering advice.
I bought a reel of flux core wire from Lidl to run test pieces, my mig can run both. A discussion with a mate at work morphed into buying the cheapest possible flux core / no gas mig welder and testing it.
£71 on eBay bought this toaster welder. Later we found the same, but different named welder for £66.
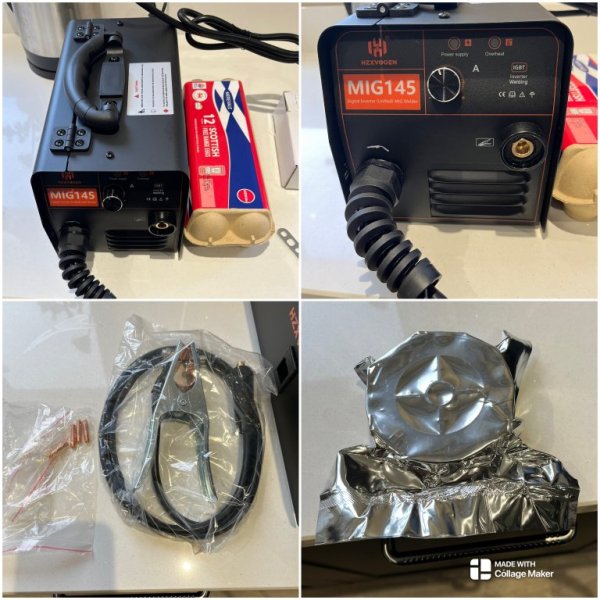
Box of 12 eggs for scale.
No readout, not even a wire speed control. The wire came well sealed, which is good, any corrosion on the wire causes chaos. Appears to have a steel liner which is also good, they last much longer than plastic liners.
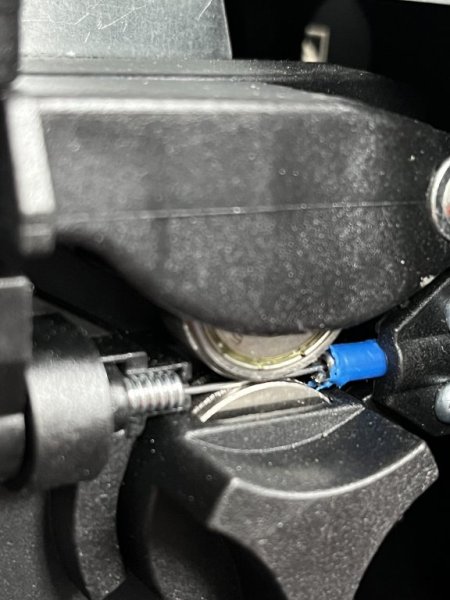
0.8 or 1.0mm wheel fitted, I might try and get hold of a 0.6mm wheel and try the reel I just bought.
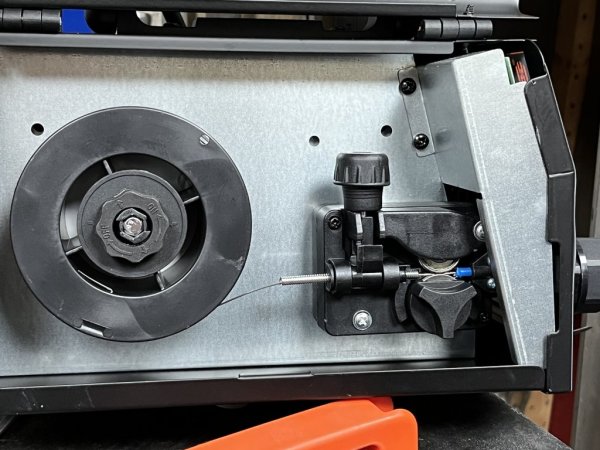
The earth cable wasn’t a great fit, 2 thin steel washers sorted that.
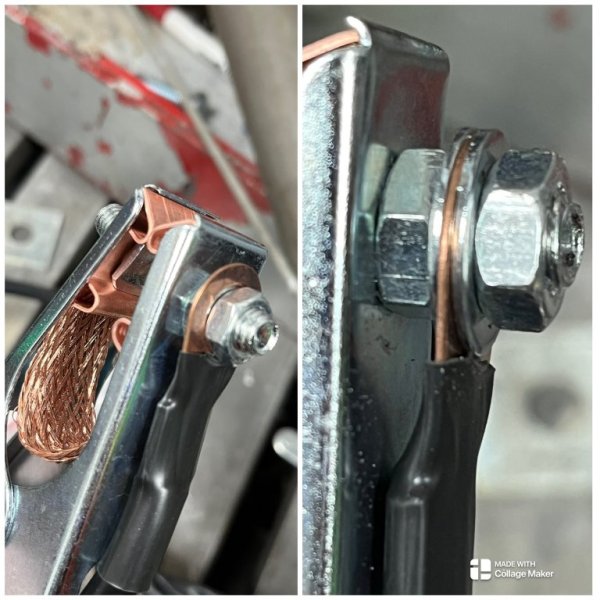
The torch is cheap, obviously, the switch is really light, I would prefer a stiffer spring. I don’t wear gauntlets, I either use tig gloves, or driver gloves, much better feel and they come in a range of sizes, gauntlets fit almost no one.
So, knowing what I’m doing, how does it weld, and how does it compare to a decent gas mig. I use a Portamig 185.
Well, first off it’s bright, tested on a piece of thick scrap I eventually settled on shade 11.5, on thin 1mm steel I went to 11.25.
I weld thin bodywork with no gap, use a technique variously called, tack and chill/zap and chill/stack-a-tack, all the same. A full penetration tack weld, immediately chilled with compressed air, or wet rag, worked across the clock. It produces minimal, if any, distortion.
Minimum setting
1
Immediately obvious, Very hot. straight through.
2
Heats up really quickly, straight through.
3
Much shorter tacks than gas, maybe 0.5s on, then 3sec off and I can run a line of tacks.
4
Same, that works.
5
I think little test strips heat up too much , even 3sec off and I’m burning through.
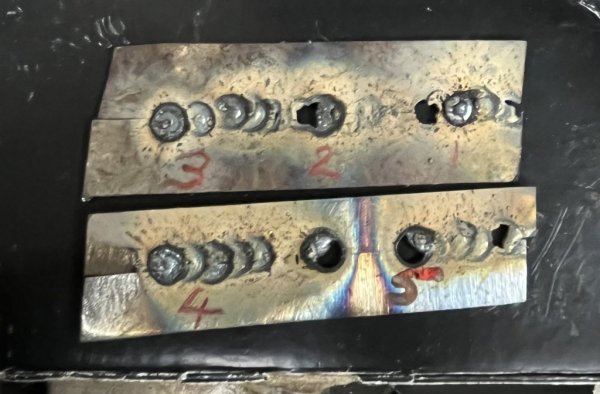
Minimal build up on the front face, it wouldn’t take much to grind flush.
Reverse side
I’m getting full penetration, I think, even on the min setting, which allegedly is 30 amps. I’m getting significant pitting, or cratering, on the back side. I need to grind the back side to see, but that will need to wait until the weekend, too noisy tonight and I only had 20 mins to test it.
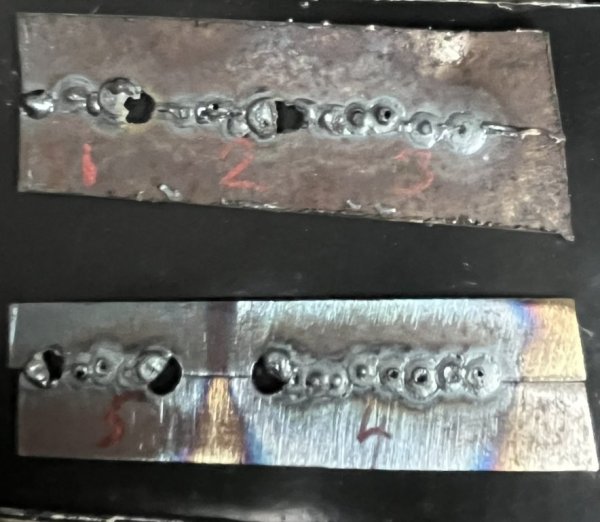
I’ll run some larger pieces this weekend in 1mm steel, same as the outer sill and some 2mm, the same as the inner sill.
Do not comment on this thread until I post after more testing this weekend. Thanks.
This should be titled:
“Having no welding experience, can you buy a flux core welder and, with a bit of practice, weld inner/outer sills to a decent standard.”
But that’s a bit long.
Matt Barnes is giving it a go in his progress thread. I can weld more than a bit, I’m not an expert, or Pro, and I’ve been offering advice.
I bought a reel of flux core wire from Lidl to run test pieces, my mig can run both. A discussion with a mate at work morphed into buying the cheapest possible flux core / no gas mig welder and testing it.
£71 on eBay bought this toaster welder. Later we found the same, but different named welder for £66.
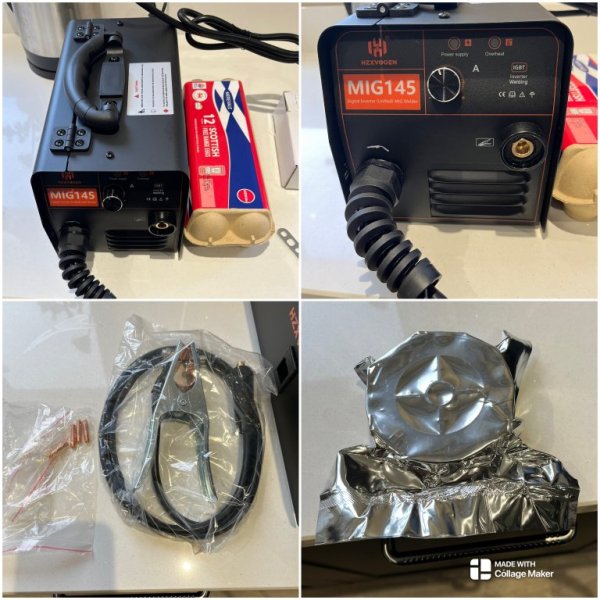
Box of 12 eggs for scale.
No readout, not even a wire speed control. The wire came well sealed, which is good, any corrosion on the wire causes chaos. Appears to have a steel liner which is also good, they last much longer than plastic liners.
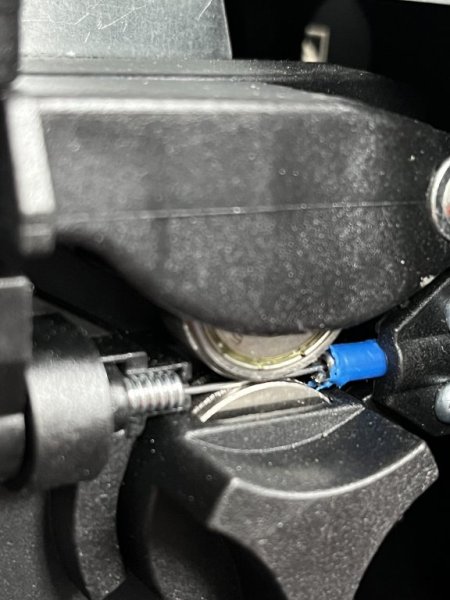
0.8 or 1.0mm wheel fitted, I might try and get hold of a 0.6mm wheel and try the reel I just bought.
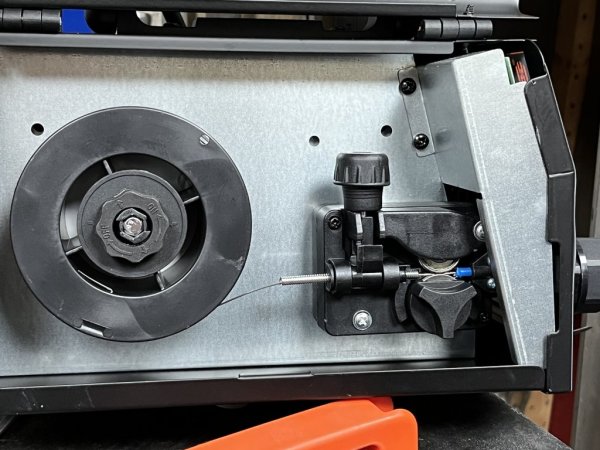
The earth cable wasn’t a great fit, 2 thin steel washers sorted that.
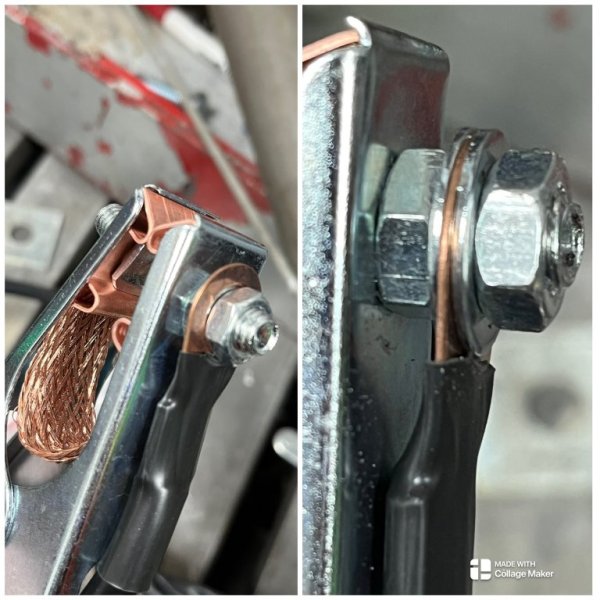
The torch is cheap, obviously, the switch is really light, I would prefer a stiffer spring. I don’t wear gauntlets, I either use tig gloves, or driver gloves, much better feel and they come in a range of sizes, gauntlets fit almost no one.
So, knowing what I’m doing, how does it weld, and how does it compare to a decent gas mig. I use a Portamig 185.
Well, first off it’s bright, tested on a piece of thick scrap I eventually settled on shade 11.5, on thin 1mm steel I went to 11.25.
I weld thin bodywork with no gap, use a technique variously called, tack and chill/zap and chill/stack-a-tack, all the same. A full penetration tack weld, immediately chilled with compressed air, or wet rag, worked across the clock. It produces minimal, if any, distortion.
Minimum setting
1
Immediately obvious, Very hot. straight through.
2
Heats up really quickly, straight through.
3
Much shorter tacks than gas, maybe 0.5s on, then 3sec off and I can run a line of tacks.
4
Same, that works.
5
I think little test strips heat up too much , even 3sec off and I’m burning through.
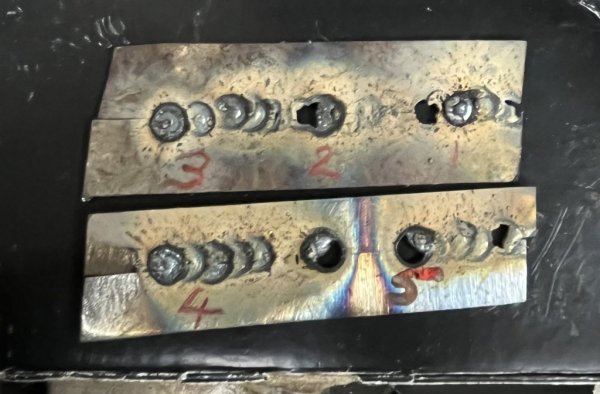
Minimal build up on the front face, it wouldn’t take much to grind flush.
Reverse side
I’m getting full penetration, I think, even on the min setting, which allegedly is 30 amps. I’m getting significant pitting, or cratering, on the back side. I need to grind the back side to see, but that will need to wait until the weekend, too noisy tonight and I only had 20 mins to test it.
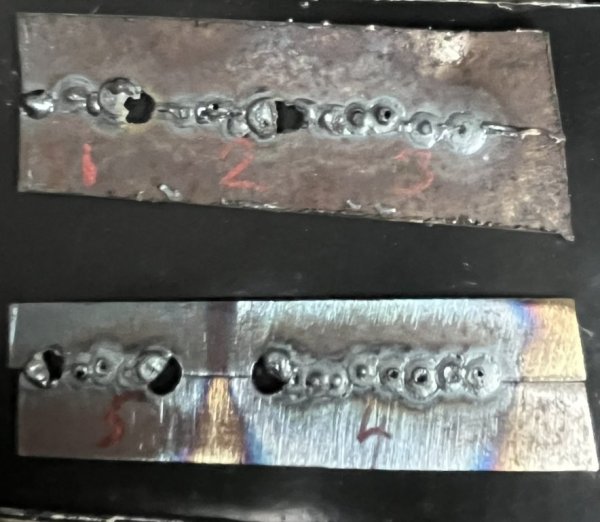
I’ll run some larger pieces this weekend in 1mm steel, same as the outer sill and some 2mm, the same as the inner sill.