I would first check with Mazza and the Zsheds to see if they have any left.
With Mazza stepping back from getting these made, perfectly understandable given the outlay, this is a quick ‘How to’ on bending your own tank straps.
NOTE: This method doesn’t end up with the two piece strap Mazza was doing, I don’t have the tools to make the kind of step required, though you could do it by welding.
TIP: Take your time. No, Really, Take Your Damn Time!
Clamp the steel and use Your Hands to bend it, it’s not all about smacking it with hammers.
Wear gloves and glasses and ear defenders when you do have to hit it with a hammer.
Tools:
Hammer, I just use a medium ball pein. Grinder or decent saw. Vice, at least 4”. Or some other method of clamping. Welder, or drill if you’re bolting the ends on. Gloves, glasses, ear defenders.
Measuring tape, sharpie marker/pencil/.
3 or 4 mm steel strip, 30-35mm wide. I would suggest 3mm for the hook end, it’s much easier.
My straps came off undamaged, so that’s what I’m using as the patterns here.
Now, the oe straps are made in 3 pieces, as you can see the ends are spot welded to the main strap.
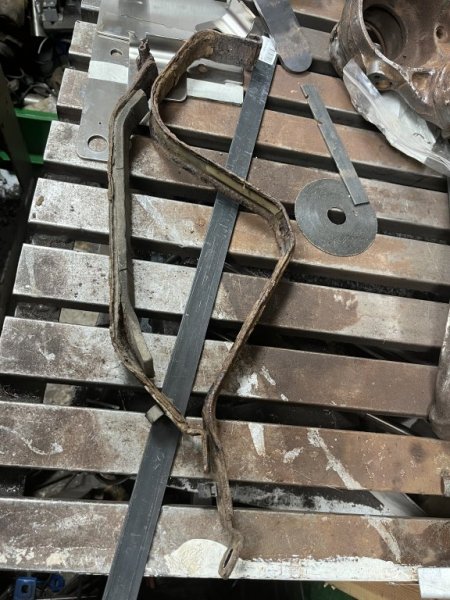
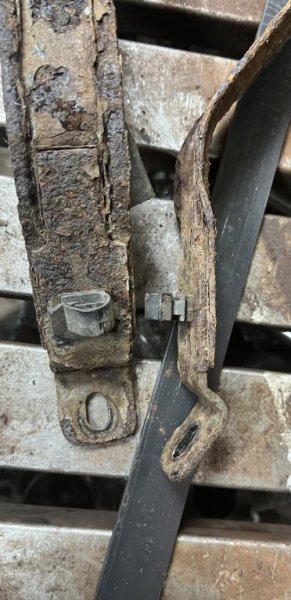
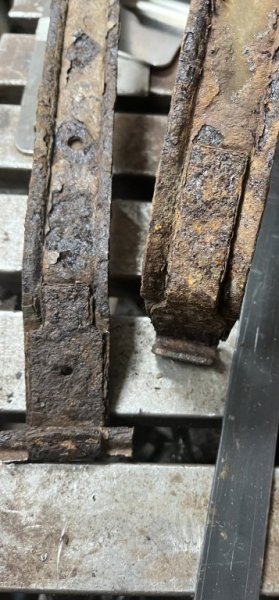
I STRONGLY suggest you do the same. Make the ends separately and either bolt, or weld, them on. Why? Because it’s far easier and gives you wiggle room for mistakes or adjustment, particularly the hook end.
Use a piece of strip slightly longer than you need, it gives you more control and allows you to finally trim to the exact size. I’m not doing that here because I don’t have enough strip of the size I wanted, so I’ve raided my scrap pile. Also, don’t use stainless, lots of reasons why, not least is you need pure argon and 316 wire.
So, the small one, two equal radius bends.
Line up the steel and mark the START of one of the bends with a sharpie. Make several parallel lines 3-4 mm apart after the start line. Now, leave your vice/clamp slightly open, I’m just using my welding table. Put your start line at the top of the vice, bend Gently with your hands, you only want to move the strip a few mm. Move to the the next line, repeat 3-4 times. Take out the strip and line up with the pattern.
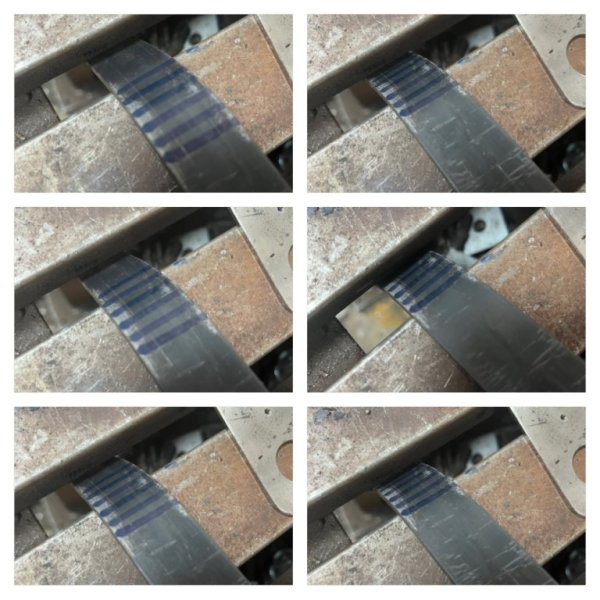
You’ll quickly see where you need to tighten the curve. It is much better to creep up on it than try to straighten it. If you find the bend has gone too far along, mark the End of the bend, tighten it level with the top jaw in the vice and straighten it. Again you should be able to do that by hand.
You should end up with this.
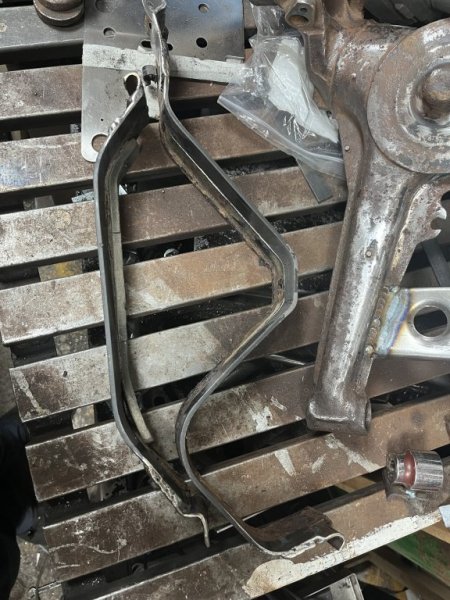
That hard part, the bendy one. DO NOT START AT ONE END!!!
The middle is the hard part, so you do that first. Mark the middle of your strip, line it up with the pattern, mark the start of one of the bends. Clamp it in the vice, put some tension on the strip with one hand and hit the strip just above the bend with the hammer. This is a tight enough radius you will not manage entirely by hand. Don’t hit directly on the bend, but just above, it needs some radius. Remove and check. Rinse and repeat until you match the bend. Once you have one done, check your mark was actually accurate, if not adjust so the second bend is going to be in the correct place and repeat.
Should give you this.
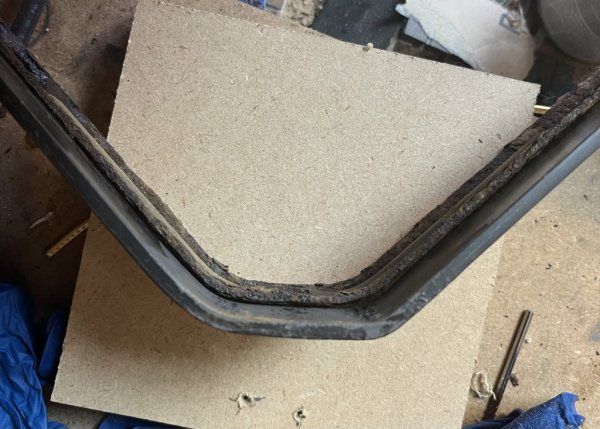
Now you’re back to doing what you did for the short one. Mark the start of the curved bend, make a series of tiny bends to make the curve. If it’s close but not quite, do not be tempted to leave it, “ahh, I’ll sort it when I’ve done the other bit” There be Dragons. Adjust it in whatever way gets it spot on. Always remember it’s easier to creep up on the curve than try and straighten then recurve it.
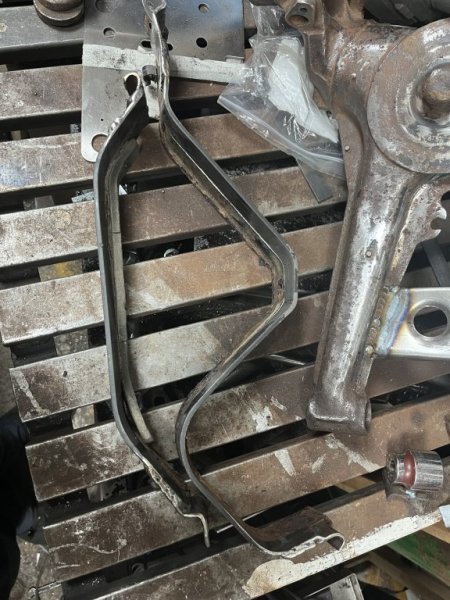
The hook end, I’d use 3mm, in fact I did, because it’s much easier to bend.
Put a piece of strip in the vice and smack it with a hammer. Do wear glasses and ear defenders. When you have a decent bend in it, add an appropriate piece of bar, or even a bolt, smack it with your hammer until it curves over, then clamp it in the vice to form a full 180 bend. Cut to length.
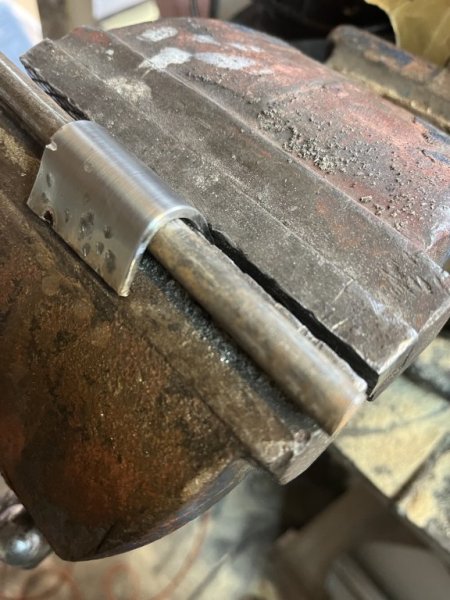
I won’t go over the bolt end, if you’ve gotten this far you won’t have any problems with that, whether you use a round hole or the elongated version is up to you.
Trim your centres to length and line up with the pattern. Adjust one end to length and clamp. Weld or bolt, up to you. If you have a hobby mig, do set it up with some off cuts, some of the little ones will probably be maxed out with two bits of 4mm. If you’re bolting it, at least two M6 with nylocs, paranoid me would use M8.
Place it back one your pattern, check it, then line up the other end, rinse and repeat.
If welded, check for spatter, remove any if present, paint, add rubber pads.
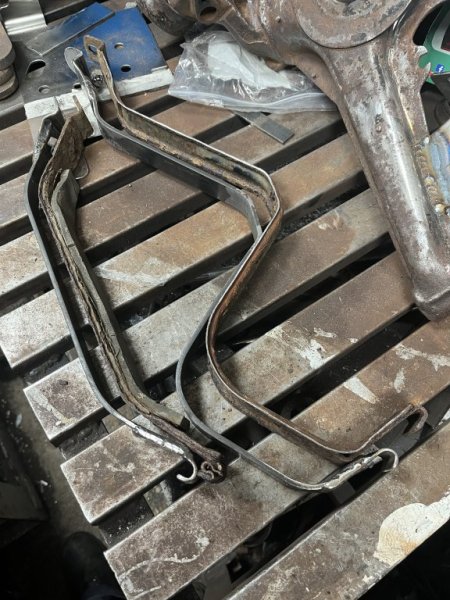
Congratulations you’ve just made yourself a set of tank straps.
I’ll edit this later as the pics aren’t showing up in the order they’ve been uploaded and I don’t have time to sort it at the moment.
With Mazza stepping back from getting these made, perfectly understandable given the outlay, this is a quick ‘How to’ on bending your own tank straps.
NOTE: This method doesn’t end up with the two piece strap Mazza was doing, I don’t have the tools to make the kind of step required, though you could do it by welding.
TIP: Take your time. No, Really, Take Your Damn Time!
Clamp the steel and use Your Hands to bend it, it’s not all about smacking it with hammers.
Wear gloves and glasses and ear defenders when you do have to hit it with a hammer.
Tools:
Hammer, I just use a medium ball pein. Grinder or decent saw. Vice, at least 4”. Or some other method of clamping. Welder, or drill if you’re bolting the ends on. Gloves, glasses, ear defenders.
Measuring tape, sharpie marker/pencil/.
3 or 4 mm steel strip, 30-35mm wide. I would suggest 3mm for the hook end, it’s much easier.
My straps came off undamaged, so that’s what I’m using as the patterns here.
Now, the oe straps are made in 3 pieces, as you can see the ends are spot welded to the main strap.
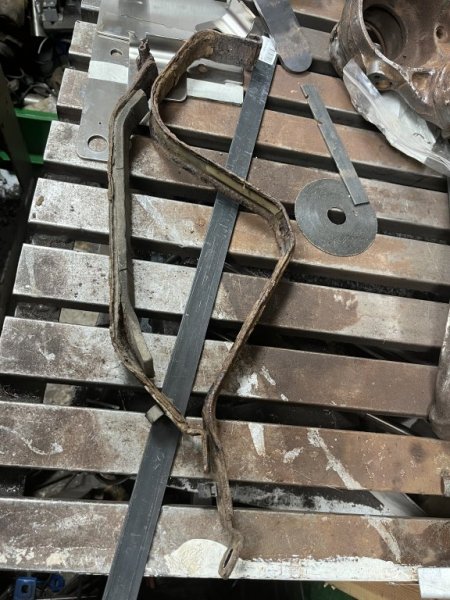
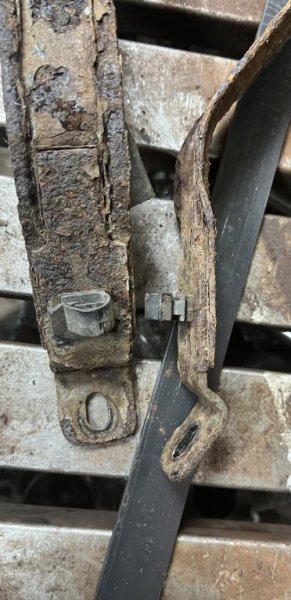
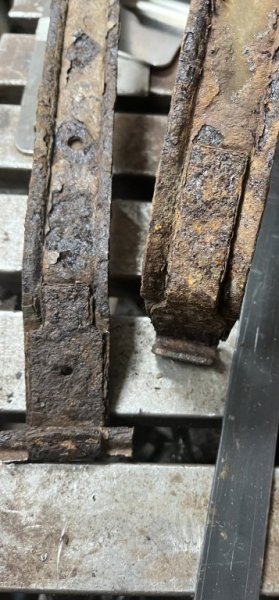
I STRONGLY suggest you do the same. Make the ends separately and either bolt, or weld, them on. Why? Because it’s far easier and gives you wiggle room for mistakes or adjustment, particularly the hook end.
Use a piece of strip slightly longer than you need, it gives you more control and allows you to finally trim to the exact size. I’m not doing that here because I don’t have enough strip of the size I wanted, so I’ve raided my scrap pile. Also, don’t use stainless, lots of reasons why, not least is you need pure argon and 316 wire.
So, the small one, two equal radius bends.
Line up the steel and mark the START of one of the bends with a sharpie. Make several parallel lines 3-4 mm apart after the start line. Now, leave your vice/clamp slightly open, I’m just using my welding table. Put your start line at the top of the vice, bend Gently with your hands, you only want to move the strip a few mm. Move to the the next line, repeat 3-4 times. Take out the strip and line up with the pattern.
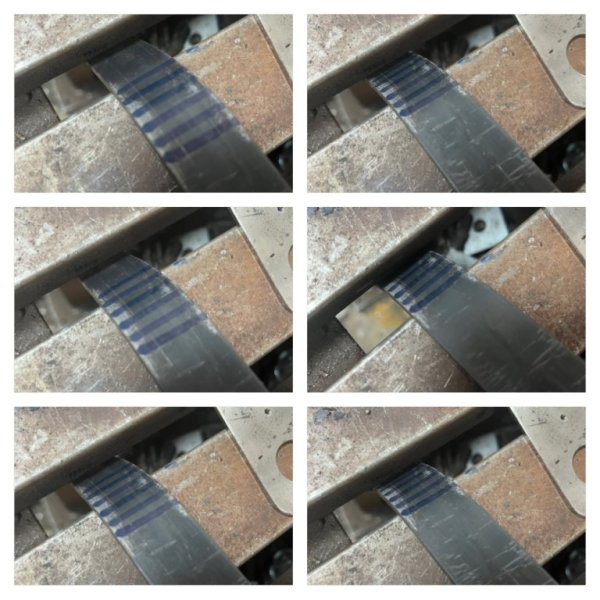
You’ll quickly see where you need to tighten the curve. It is much better to creep up on it than try to straighten it. If you find the bend has gone too far along, mark the End of the bend, tighten it level with the top jaw in the vice and straighten it. Again you should be able to do that by hand.
You should end up with this.
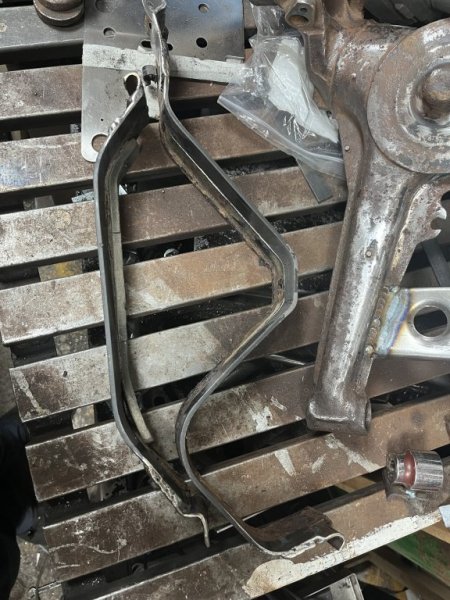
That hard part, the bendy one. DO NOT START AT ONE END!!!
The middle is the hard part, so you do that first. Mark the middle of your strip, line it up with the pattern, mark the start of one of the bends. Clamp it in the vice, put some tension on the strip with one hand and hit the strip just above the bend with the hammer. This is a tight enough radius you will not manage entirely by hand. Don’t hit directly on the bend, but just above, it needs some radius. Remove and check. Rinse and repeat until you match the bend. Once you have one done, check your mark was actually accurate, if not adjust so the second bend is going to be in the correct place and repeat.
Should give you this.
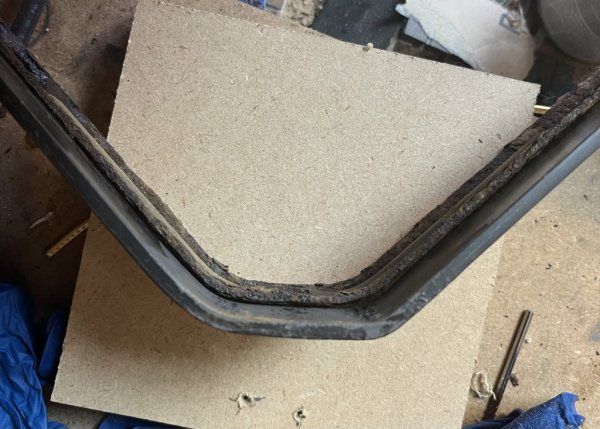
Now you’re back to doing what you did for the short one. Mark the start of the curved bend, make a series of tiny bends to make the curve. If it’s close but not quite, do not be tempted to leave it, “ahh, I’ll sort it when I’ve done the other bit” There be Dragons. Adjust it in whatever way gets it spot on. Always remember it’s easier to creep up on the curve than try and straighten then recurve it.
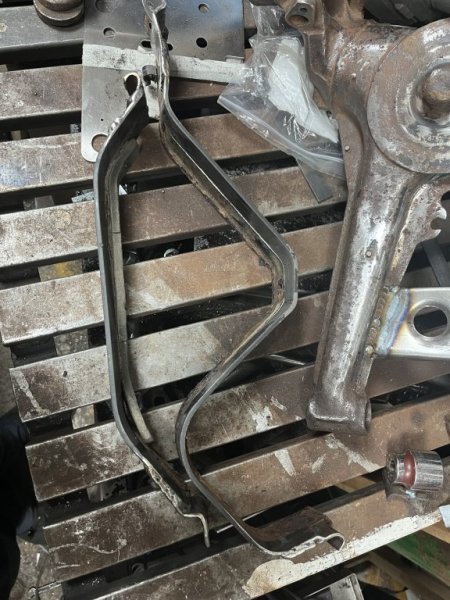
The hook end, I’d use 3mm, in fact I did, because it’s much easier to bend.
Put a piece of strip in the vice and smack it with a hammer. Do wear glasses and ear defenders. When you have a decent bend in it, add an appropriate piece of bar, or even a bolt, smack it with your hammer until it curves over, then clamp it in the vice to form a full 180 bend. Cut to length.
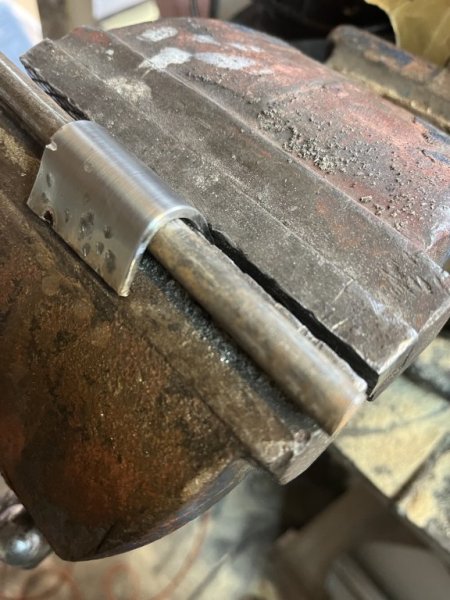
I won’t go over the bolt end, if you’ve gotten this far you won’t have any problems with that, whether you use a round hole or the elongated version is up to you.
Trim your centres to length and line up with the pattern. Adjust one end to length and clamp. Weld or bolt, up to you. If you have a hobby mig, do set it up with some off cuts, some of the little ones will probably be maxed out with two bits of 4mm. If you’re bolting it, at least two M6 with nylocs, paranoid me would use M8.
Place it back one your pattern, check it, then line up the other end, rinse and repeat.
If welded, check for spatter, remove any if present, paint, add rubber pads.
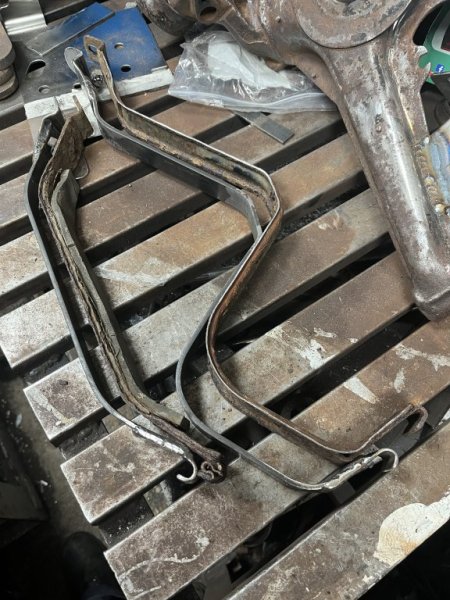
Congratulations you’ve just made yourself a set of tank straps.
I’ll edit this later as the pics aren’t showing up in the order they’ve been uploaded and I don’t have time to sort it at the moment.
Attachments
-
91.8 KB Views: 15
Last edited: